Blog / Insights
What is Value Engineering in Construction?
THE TRUTH ABOUT VALUE ENGINEERING
Picture this: You’ve collaborated with your interior design team to create your ideal space. You’re getting your employees, partners, customers, or community pumped about the project. You request bids from a range of general contractors, eager to turn this beautiful concept into a reality. However, the bids are far greater than you imagined.
Is it time to brutally “value engineer” your project in order to save costs? No, not always. When we hear the phrase “value engineering,” we instantly think of a process that minimizes the cost of a project by eliminating sections or lowering the grade of materials utilized. However, it is not always the case with value engineering.
What Exactly Is Value Engineering in Construction?
Construction Value Engineering is a systematic, planned value-adding strategy to providing essential functionalities in a building project at a lower cost. Value engineering encourages the replacement of less costly materials and technologies without affecting functionality or overall . It is primarily concerned with the functionalities of various components and materials, rather than their physical characteristics. Value engineering is often referred to as value analysis.
KEY TAKEAWAYS
- Value engineering is a systematic and coordinated construction service that focuses on supplying the required functionalities in a project at the lowest possible cost.
- Value engineering encourages the replacement of less costly materials and processes without losing functionality
- Construction Value Engineering focuses entirely on the functionalities of various components and materials, rather than their physical qualities.
RECOGNIZING VALUE ENGINEERING
Value engineering is the process of reviewing new or current materials throughout the design phase in order to minimise costs and expand functionality in order to make a commercial construction project more-efficient. The value of an object is defined as the most cost-effective method of producing it without sacrificing its function. As a result, decreasing money at the price of quality is only a cost-reduction technique.
Cost reduction should not have an impact on the quality of the product being developed or studied while using value engineering. During World War II, the notion of value engineering emerged at General Electric in the 1940s.
Because materials and components were in short supply due to the war, purchasing engineer Lawrence Miles and others looked for replacements. These replacements were frequently discovered to be less expensive while providing similar or superior performance.
ESTABLISHING “VALUE” FOR YOUR PROJECT
A good value is defined as anything that has a positive cost-benefit ratio. While it may appear that expenses are simple to quantify – how much they cost upfront – there is a bit more to them. To truly grasp the significance, you must delve deeper. How long can the materials be expected to last? What kind of upkeep will they require? Will they be more efficient and less expensive to run? The best way to begin is by asking yourself what the most essential part(s) of the project are, and what you want the project to accomplish.
Once you’ve established them, share them with your value engineering team, and they’ll respond with a list of ideas that respect your goals while also improving your project to give the most possible value while staying within your budget. This strategy focuses on adding value to your specific project rather than broad cost-cutting strategies that may not be the greatest fit for your requirements or goals. A strong construction value engineering team will analyze everything and find you the greatest quality choices at the lowest possible cost.
Keep the following three major factors in mind while considering these suggestions: cost savings, increased quality, and life cycle/maintenance.
LOWERING THE COSTS / CONSTRUCTION COST SAVINGS
Many value engineering techniques are motivated by a desire to reduce overall construction costs. Your commercial general contractor can suggest less-expensive materials for your consideration and give you an idea how much you could save with that specific option. Whether it’s locating a less expensive fixture or replacing a redundant feature, these tips can add value to your project.
However, without the following requirements, construction value engineering would just be referred to as cost-cutting. Added quality guarantees that cost cutbacks do not reduce the project’s value.
INCREASED QUALITY
Quality must be considered before making any decisions about your value engineering solutions. Quality can refer to a variety of things. The standard of the environment you’re creating. The standard of the items that comprise that environment. The calibre of the team you’ve assembled to create that environment.
While certain equipment or design aspects may be more expensive, they may be justified by the quality that they provide. Higher-priced components and elements may enable you to demand a higher fee for your services. They may improve the productivity or satisfaction of those who will utilize the place. A high-quality product may have more total value than a low-cost product.
MAINTENANCE/LIFE CYCLE
Similarly to quality, it is critical to evaluate the long-term consequences of these value engineering initiatives. While low-cost flooring may appear to be the most cost-effective option at first, if you have to replace it twice as frequently as higher-cost flooring, it may wind up costing you more money in the long term. However, if saving that extra money upfront is the difference between getting your idea off the ground and it stalling in design, then making that decision may be the best option.
At GTA General Contractors, we specialize in finding quality and cost-efficient materials that meet or exceed the performance of the material to be replaced, so you can be sure that material will perform in the long-term.
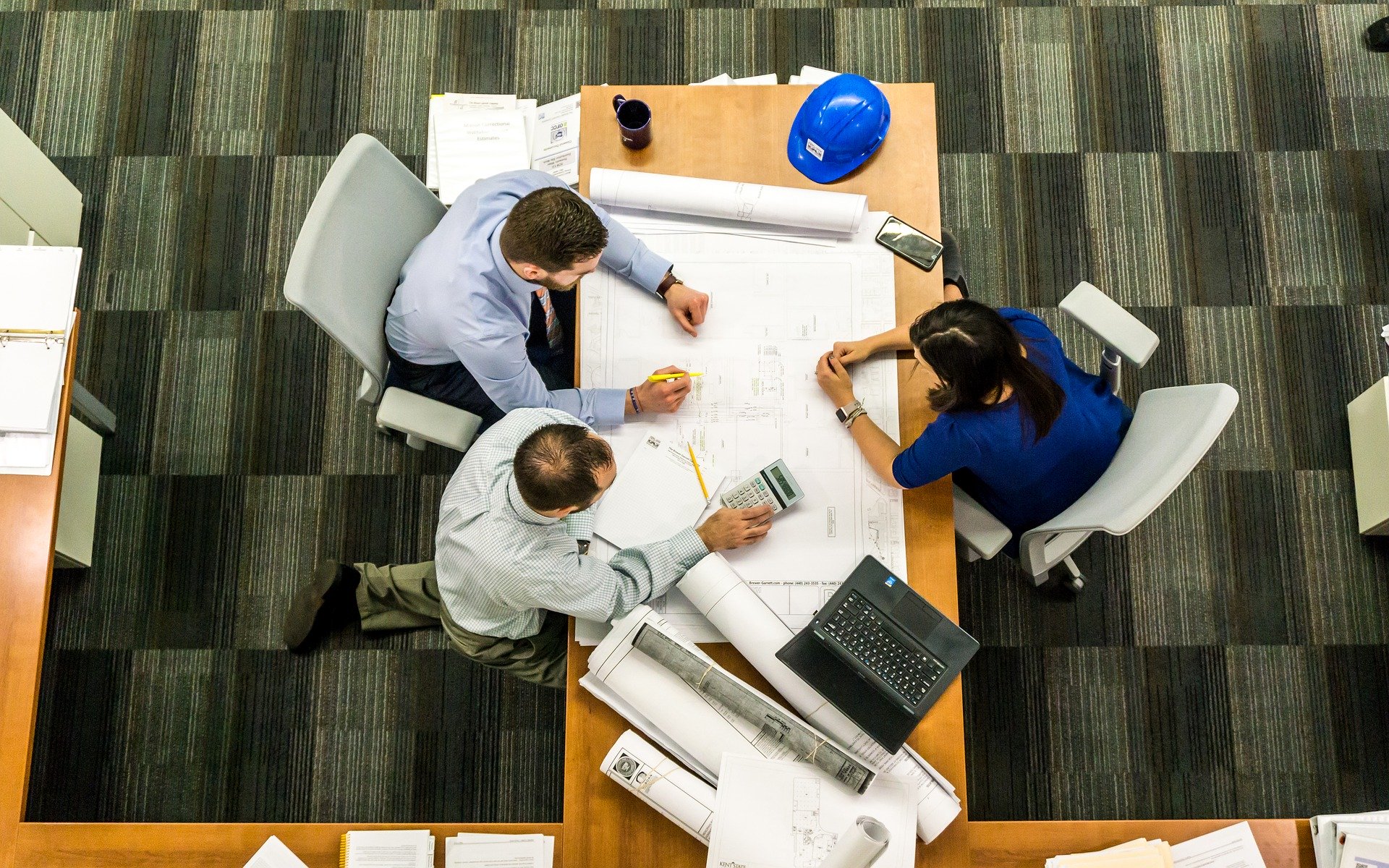
WHEN SHOULD VALUE ENGINEERING BE PERFORMED?
A construction project is divided into three stages: project planning, design, and construction. As the owner, you have the option of requesting value engineering services at any moment during the commercial building process. However, the benefits and drawbacks of making adjustments differ depending what stage you are in.
ENGINEERING FOR VALUE DURING PROJECT PLANNING
In most circumstances, the optimal moment to value engineer is during the planning stage of your project. The cost of implementing these adjustments will be the lowest, and the impact on the project’s timeline will be the smallest.
At this point, your value engineering team will inspect the facility and collaborate with you to develop your project vision and objectives. With this information, they will be able to provide you with options that will work for your project. They will then incorporate them into the project plan in a seamless manner.
While this involves more upfront planning, it can spare you from costly change orders that might cause your project’s timetable to slip later on. During project planning, construction value engineering is used.
ENGINEERING FOR VALUE DURING THE DESIGN PHASE
Value engineering occurs during the design phase of most typical projects. The owner collaborates with an architect to create construction papers, which are subsequently utilised by contractors to create estimates. When those estimates are found to be too high, the project team goes back to the drawing board (literally) and begins searching for methods to save you money. However, it is important to emphasize that value engineering should not be limited to cutting building costs. The value engineering team must consider long-term expenses as well as the overall value of the project in order to provide recommendations that are in line with the owner’s goals. One disadvantage of performing the majority of your value engineering during the design phase is that you may incur redesign expenditures.
ENGINEERING FOR VALUE DURING THE CONSTRUCTION PHASE
Just because boots are on the ground and work is underway does not mean that your project team should stop reviewing the project. Through value engineering change orders, value engineering may continue while work is put in place with ideas from your preferred commercial general contractors.
However, because building has already begun, revisions to the designs can be expensive and may lead the project to go behind schedule. All value engineering proposals made during this phase must be evaluated seriously in order to comprehend the entire impact of the change on the project.
That is why it is critical to work with a cost-efficient commercial construction company that is dedicated to doing the right thing and being valuable construction partners. GTA General Contractors will be an active construction partner from the beginning to the end of the project. We will never stop looking for methods to maximize the value of your building project.
Contact Us
Looking for more construction insights? Our team is here to help!
We’re here to help our people, our clients, and our communities achieve their ambitions. Let us know how we can help, or what you’re looking for, and one of our experts will be contact you promptly